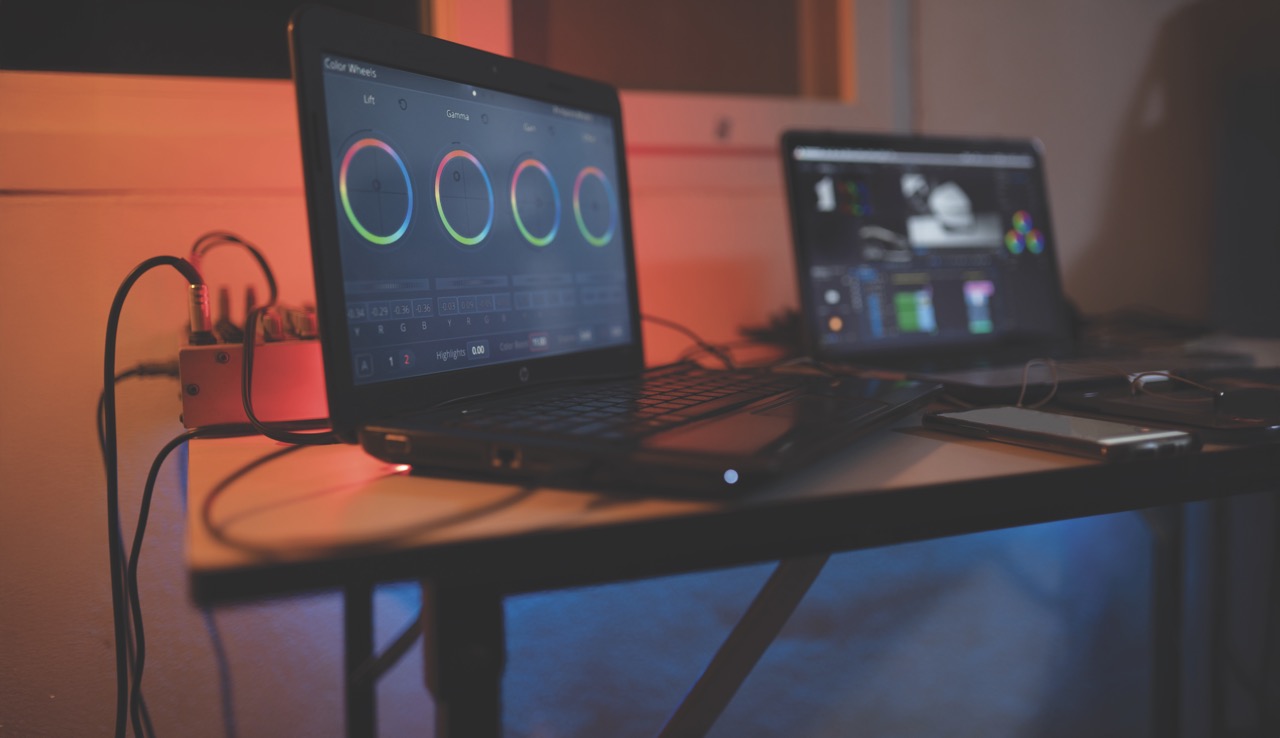
Colour special: Glass to glass through colour control
Posted on Jul 17, 2025 by Admin
Colour control is more powerful – and complex – than ever before. Phil Rhodes explores the tools shaping how we see the image
Words Phil Rhodes
Moving a picture from lens to TV has often been described as going from glass to glass. The phrase has always involved a little idealism; no camera-display combination has ever tried to recreate the real world photon by photon.
The way colour makes it through the system has always involved opinion, and the technology has recently made that process much more flexible. At the same time, creative inspiration most often arises from productions old enough to have become classics, made when colour control was – from the cinematographer’s perspective – just simpler.
Nobody is second-guessing the colorimetry of Lawrence of Arabia just because it was made without a dozen different monitoring LUTs.
Current technologies tend to have equivalents in history. Film stock changes now happen at the press of a button. The duties of a DIT overlap, broadly, with the traditional lab contact. Gaffers who might once have prepped correction filters for each HMI find themselves dialling in colour using a chart designed for physicists. All that flexibility has moved a lot of complexity from lab to set, where time is expensive.
In the end, all of this arises from two huge changes in cinematography: digital acquisition and LED lighting, which took place against a backdrop of more general changes in display and post-production technology. Colour has changed in fundamental ways – and the pace of that change has been rapid for a decade or more.
Now, though, the world seems almost relieved at signs of maturity, as product design has begun to involve something other than a race for competitive numbers.
On lighting
Until we have 18kW LEDs, there will continue to be a mountain to climb. Still, more conventional power levels matter to more people, and new releases often compete on features as much as anything else. The biggest issue, though, remains colour quality – and that’s not a new issue at all.
New ideas are often pushed onto the market when the underlying technology is barely capable of doing what is asked of it. That, and a dubious public understanding of how colour works, was no great help to emergent LEDs. Perhaps people knew that combining red, green and blue light does not create white light; it just looks like white light – at least when it illuminates colourless objects. Illuminate a sunflower with an RGB disco light, and the dull, underwhelming result makes it clear that there is no yellow in our putative white.
What we want is the glow emitted by hot things. Candle flames, tungsten-halogen bulbs and stars are all bright because they are hot. LEDs are not, although they can often pretend fairly well. Having a blue LED illuminate a yellow-emitting phosphor – as has been common for years – is a mature technology. Even affordable options can now produce reasonable whites.
Does it create a spectrum which looks exactly like a tungsten-halogen light bulb? No, but neither do fluorescent tubes and HMIs. The difference might be that (quality) fluorescent tubes and HMIs create a spectrum with few complete voids – there is some light of almost every colour. LEDs have often lacked deep reds and blues.
Accordingly, designers have started to include deep-blue emitters that, surprisingly, improve skin tones. Collagen and elastin glow slightly under near-blacklight. At the other end of the spectrum, emitters with phosphors engineered specifically to convert blue emitters to deep red are sometimes used. Humans are mostly warm colours because they are full of deep-red blood.
This is great. Is it the new essential?
Perhaps one day, but conventional yellow-phosphor-on-blue LEDs have an enviable track record. What’s more, a ruby-coloured phosphor red LED is less efficient than a more vermilion-leaning, non-converted red emitter. Other configurations offer different compromises and different colour capabilities, and we trade efficiency for capability.
In 2025, a working knowledge of those choices is likely to be useful to everyone, but the question is not so much quality as consistency. Different approaches can and do visibly vary, even when asked for the same thing. The only solution to matching, so far, has been an eyeball.
Displays and consistency
Making things look the same is a problem for both gaffers and DITs, although the latter tend to have better tools. Expectations can be sky high, with two monitors expected to be indistinguishable. But even if they are, fundamental limitations of monitoring arise from human vision itself. It can be exquisitely sensitive; side-by-side comparison of two displays (or lights or fabric swatches) allows humans to see variations better than the measuring instruments used on film sets.
Conversely, evaluating colours in isolation is something that humans do poorly. Show a human a colour, then ask that human to pick that colour out of a series of similar colours, and it becomes clear that our colour memory decays in seconds. Change the ambient lighting and things get even flakier. In the grading suite, precision is everything – but out on location, compromise is inevitable. The need for accuracy, then, is to keep the human perception as honest as possible.
Monitoring is a field in which film and TV inherit tech from adjacent industries. The bonanza of small, high-quality on-camera monitors relies entirely on the huge resources of mobile phone manufacturers. OLED, likewise, was a difficult, thoroughbred technology that only exists because of domestic TVs. Recent quantum-dot OLEDs – which use glowing compounds to create colours in a way analogous to LED lights – have brought unprecedented performance to both domestic and professional users.
The problem is that new ideas inevitably encounter the incumbent technology when it is already well developed. Matching LCD contrast performance to an OLED demands the dual-layer panels now offered for precision reference applications. How this might end remains to be seen, but it is worth remembering that LCD has already vanquished the plasma display.
Glass to eyeball
For the first time in the history of TV, home users can now see images that closely match those viewed in the grading suite – especially with filmmaker mode enabled. The difficulty for production teams is that, in the past, there was mostly one way to prepare images for film and one for TV. Now, different distribution formats demand varied standards, which differ by design.
Overworked colourists facing a fourth trim pass on the same show might start to lose enthusiasm. Still, people do appreciate HDR done well, and that might make us think again about the words ‘glass to glass’. After all, that omits two crucial parts of the system: the lights at the start of the process, and the eyeball at the end.
This article appears in the July/August 2025 issue of Definition