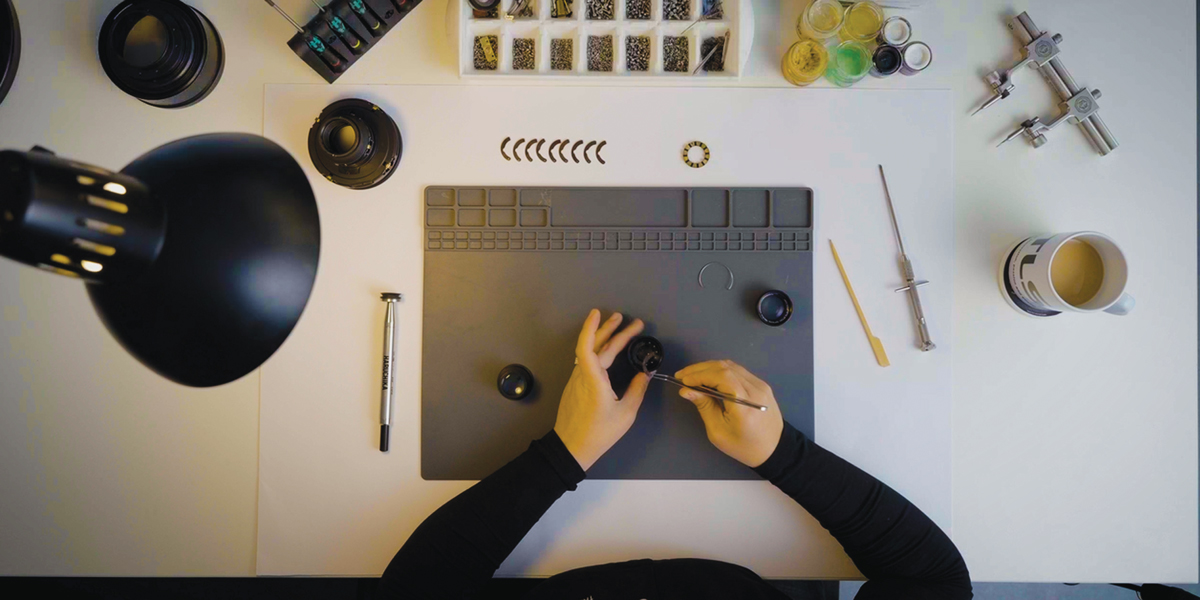
Classics Reborn: Lens Rehousing
Posted on Jul 27, 2024 by Samara Husbands
Nicola Foley digs into the rising trend of rehousing vintage cine lenses
Modern cine lenses are a feat of optical engineering: optimally designed and capable of delivering perfectly clean, consistent and sharp imagery with excellent contrast in each and every shot. But in a world where we can get our hands on pretty much perfect lenses – for the right price, at least – many cinematographers hanker for that distinctive aesthetic only vintage glass provides.
That dreamy bokeh and nostalgic softness, those charming flares and the delightfully unpredictable imperfections – like subtle chromatic aberrations, which give footage an organic, textured feel. An increasingly popular solution that blends the best of both worlds is rehousing classic lenses, which offers the tantalising combination of the precision and reliability of modern technology combined with the unique character of vintage glass.
“Many people are drawn to the aesthetic look that vintage lenses give, and rehousing is a smart investment for filmmakers who want to harness the unique visual characteristics of older optics, while upgrading their functionality to meet modern production standards,” sums up Gary Leach, lens engineering manager at CVP.
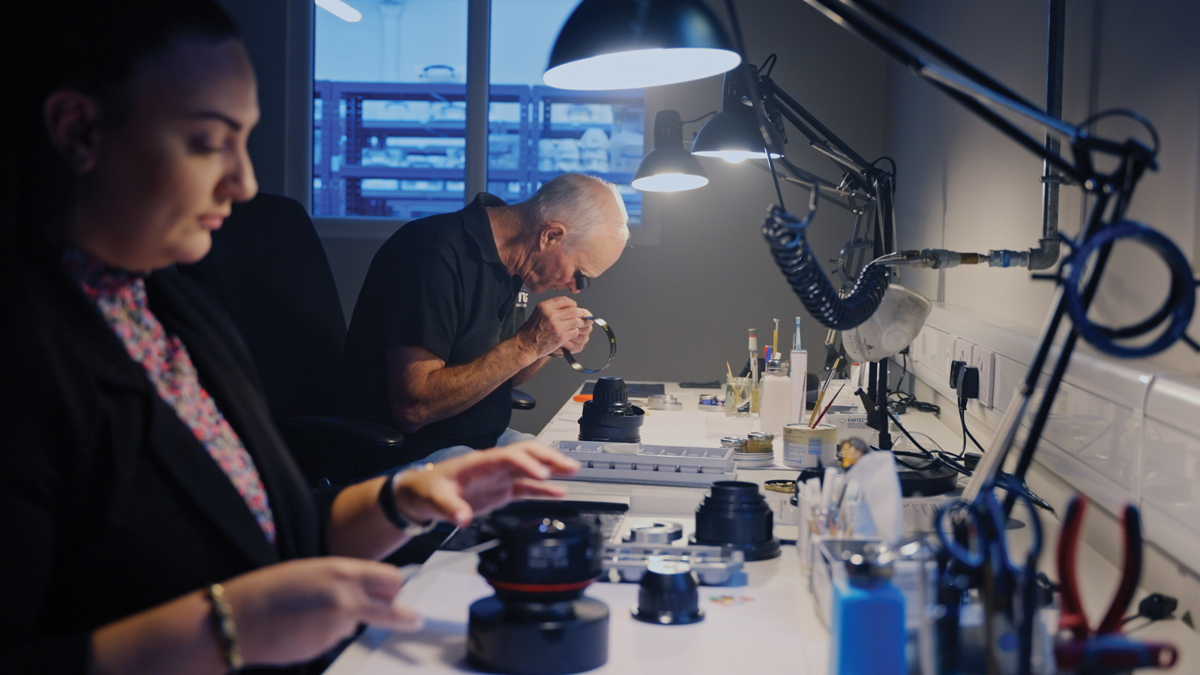
Back to the Future
By removing the glass (and sometimes the iris as well) and building it into newly engineered mechanics, rehousing allows you to use your favourite vintage optics efficiently with modern equipment. “Apart from the look, one of the key reasons will be the change of lens mount – usually to PL – which provides compatibility with current camera models,” Leach adds. “Rehoused lenses can also include the addition of accurate focus scales and gear rings for remote drives, allowing for improved focus control. This is particularly beneficial for remote focus pulling.”
It’s easy to see the appeal. True Lens Services (TLS), based in Leicestershire, UK, is one of the world’s top specialists in the field of converting, servicing and repairing lenses for film and TV – and the team reports a ‘tremendous amount of growth’ in requests for the rehousing of vintage optics over the last five years.
In the early days, one of the key drivers for this was the switch to digital sensors, which are becoming increasingly sharp, along with the lenses. “The image was just too sharp for some things,” explains Gavin Whitehurst, managing director at TLS. “That’s great for sports or wildlife, but when you’re seeing makeup and wrinkles on people’s faces, going back to vintage is a nice way of breaking up that image slightly with a softer look and the coatings. Things like lead in the glass gives that certain sparkle.”
“We saw steep growth initially when the full-frame sensors came out,” adds the firm’s director of operations Stephen Lowe. “Canon K35s were the only true vintage cine lenses which would cover the full-frame sensors from 24mm and onwards – but that opened up a world of stills photography lenses; many of these will cover that format, since that’s what they are designed to be used with. You can use vintage stills lenses with current cameras which can compete with new, modern-day glass – potentially at a lower price as stills lenses were relatively cheap to buy.”
That said, the process of rehousing doesn’t come cheap. You’re looking at around £5k (at least) for a rehousing service, and this intricate, artisanal process takes time. TLS estimates a typical timeline of around ten weeks from start to finish – and currently has a waiting list of around six months, depending on the lens type and demand.
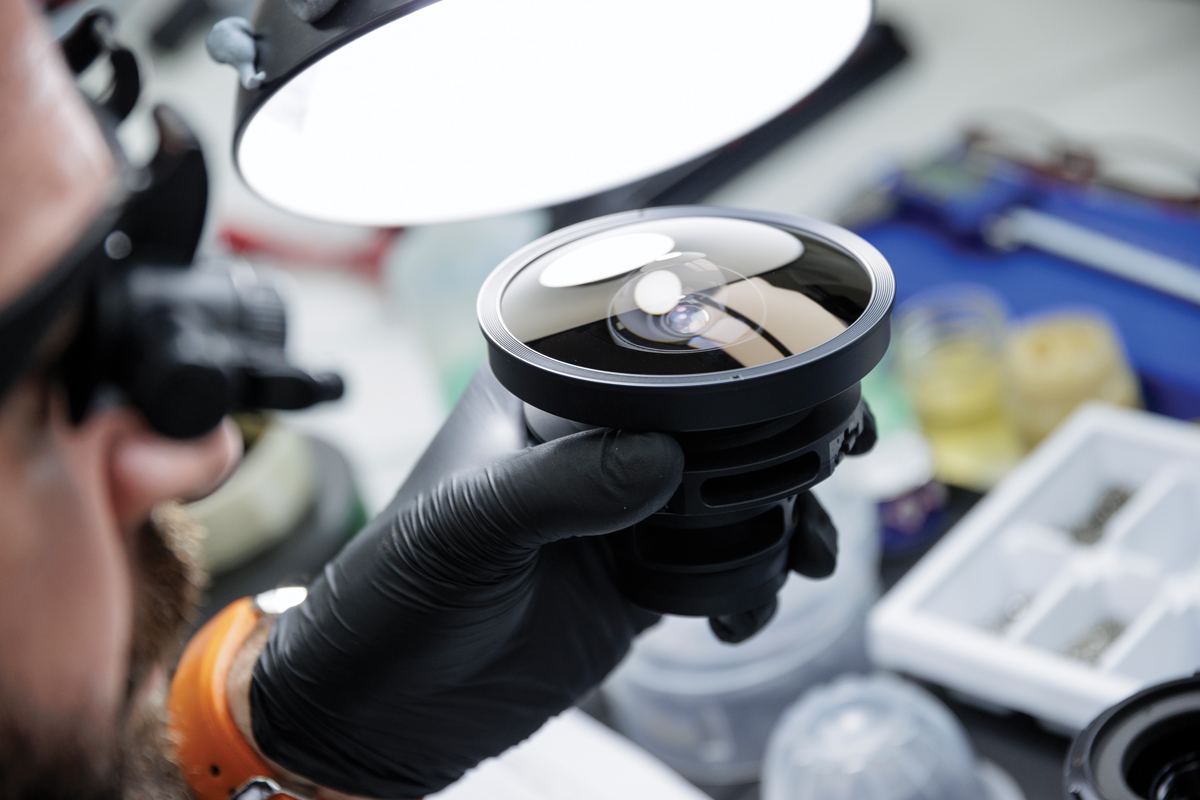
Unlocking Vintage Potential
If you have the time, money and perfect donor glass for a reno job, the next step is getting a thorough inspection and quote. At this point, technicians can assess if any additional work – such as deyellowing, edge blackening and recementing – needs doing. Assuming they are happy with the condition for rehousing, it’s full steam ahead.
Next, explains Lowe, the lens gets fully disassembled. The optics and iris (if it doesn’t need replacing) are meticulously cleaned, before getting loaded into new metalwork. After that, the lens will be built up to a stage where you can set the back focus and check and align the image. “Once we’re happy the image is as expected and within specification, there’s a final clean and full assembly with all the blank sleeves on,” continues Lowe. “We then set the back focus again, take the lens into the projection room and mark up the focus scale individually, so each mark on every focus scale is done individually. The iris is done on the T-scale bench to make sure we get accurate aperture readings.”
TLS will then remove and engrave sleeves, build the lens back up into its final form and give it back to the technician, who completes a last check and ensures the whole set matches and feels consistent, before a final QC. Once it gets the stamp of approval, it’s time for the newly revitalised lens or lenses to be shipped out to the customer.
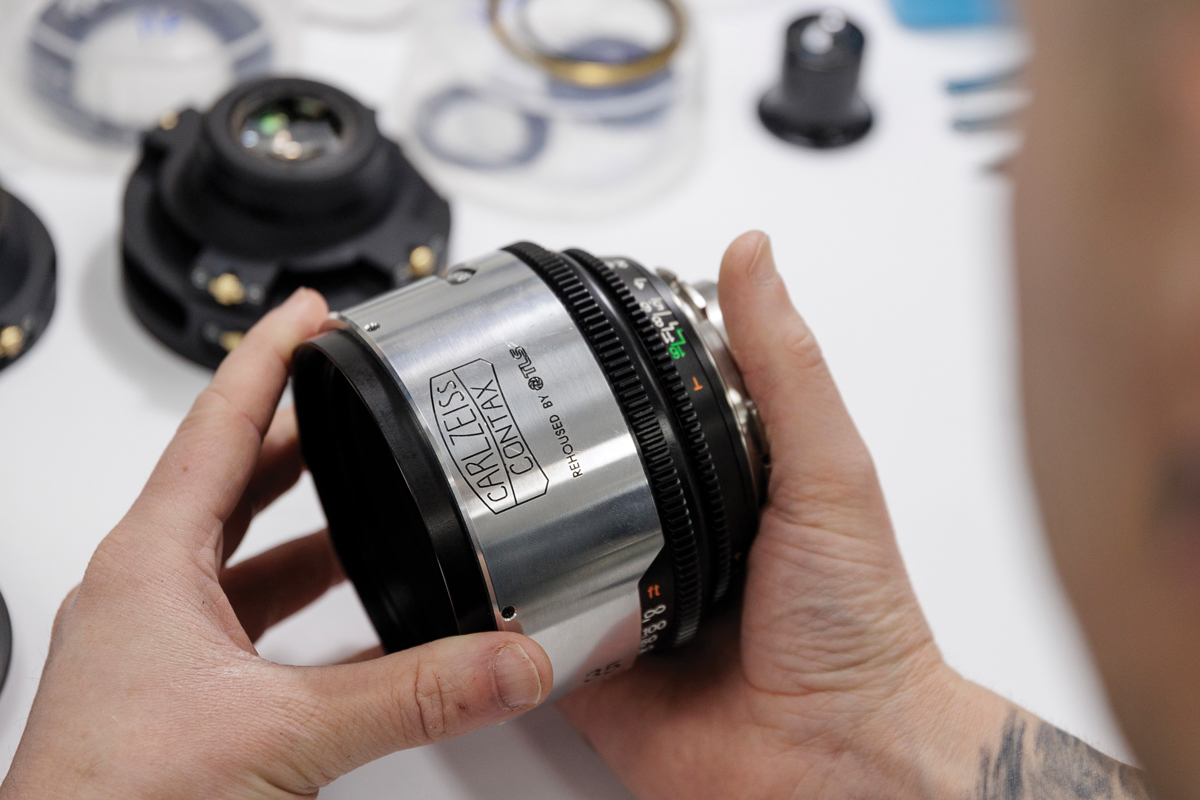
When can’t you rehouse a lens?
The process can throw up issues; Leach points to intricate designs that are tricky to disassemble and reassemble as well as the availability of parts – both of which are surmountable in capable hands. Meanwhile, Whitehurst says floating elements (where there are one or more groups of elements moving at a different rate to one another) present hurdles in ensuring everything is correctly aligned. To tackle this, TLS uses a variable cam system which allows for fine adjustments – a feature not universally employed by other rehousing companies.
But are there situations where rehousing is simply not possible? “If you have enough money and can find someone willing with the time, then any lens can be rehoused!” assures Leach. TLS cautions, however, that occasionally a lens is so badly damaged – or has a fungus problem so severe – that a client might not get the result they are hoping for.
If they still want to go ahead? “We’ll give feedback, let them know the faults with the lens, then advise them on the work,” says Whitehurst. “Sometimes, a lens needs replacing. If a client still wants that lens rehousing, as long as we think we can mark it up, we’ll be clear about the limitations and do it if they want to.”
Glass Act
Another point in the pros column for rehousing is the simplicity of maintaining them, claims Leach. “Servicing an old lens which has been rehoused can be much easier than servicing the original lens because the mechanisms in modern housings are usually simpler in design. Present-day designs employ advanced machining capabilities as well as modern materials, enhancing simplicity and ease of maintenance. These improvements will also boost durability – extending their life and usability.
“Many old lens housings are damaged by years of use, servicing and people using the wrong tools, making them hard to dismantle,” continues Leach. “Additionally, since many old housings are worn out – leading to problems like backlash and alignment issues – they often don’t feel very nice. Rehousing enhances the handling and overall feel of these lenses, addressing these issues and improving their performance.”
According to CVP, popular rehousing projects include IronGlass’s refit of the Helios, Soviet and Carl Zeiss Jena lenses. Additionally, the Canon K35, Zeiss Super Speed, Canon FD, Leica R, Mamiya 645, Kowa Cine PROMINAR and Cooke Speed Panchros are also favourites.
The latter was TLS’s first rehousing project, proving to be hugely popular. Having only originally planned ten sets to justify the design time, the team has now worked on around 500 sets of these lenses. The team also sees big demand for the Canon K35s, largely due to being one of the only vintage cinema lenses to cover full-frame.
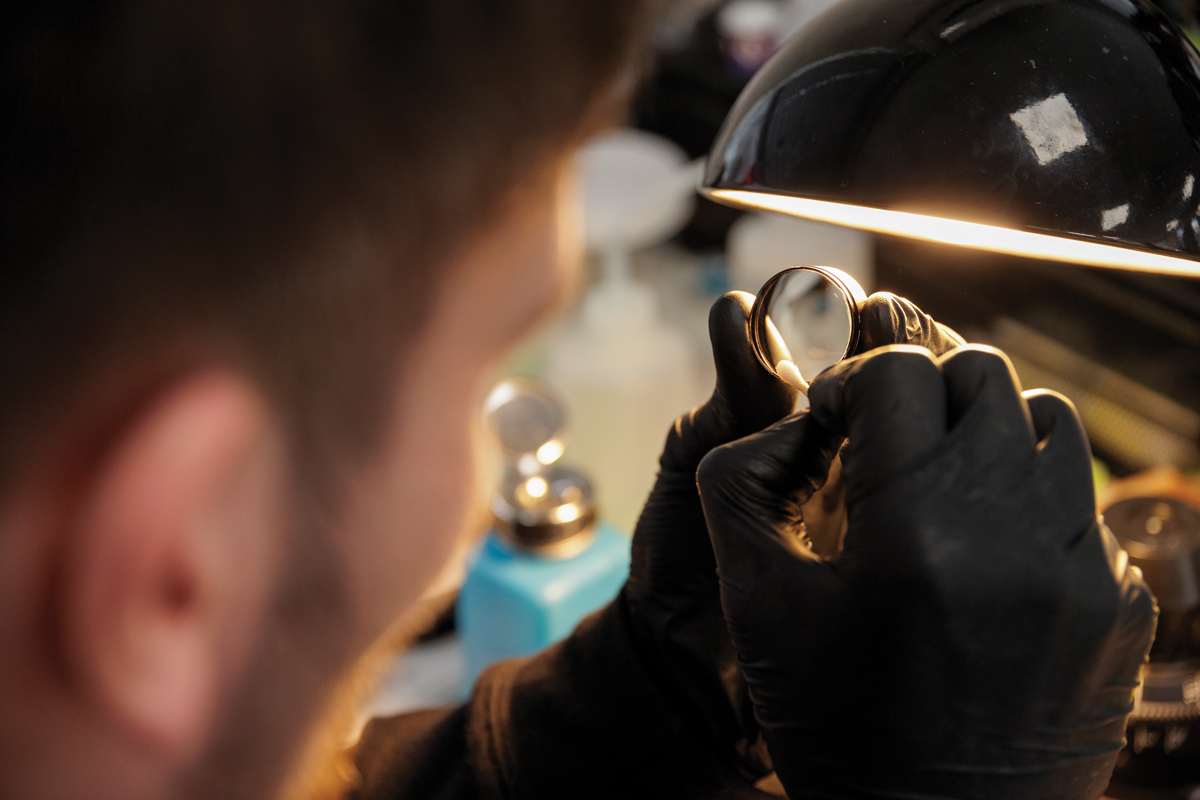
What’s next for rehousing?
Looking to the future, TLS is keen to continue refining its housing designs, striving for improvements in serviceability and functionality with each iteration. While technology is evolving rapidly around us, the team can’t see a world in which craftsmanship and expertise are replaced by machines.
“That’s probably the reason we’ve stayed successful; it is quite an artisan process. I don’t think there’s any kind of shortcut to what we do,” muses Lowe. “I doubt machinery will be able to replicate what the guys are doing with the assembly. It will be interesting to see what happens with regards to AI and the industry as a whole – whether it makes post-production much easier and more efficient to have these effects outside of the cameras, rather than in-camera. But right now, it’s very much the trend that everybody wants to create the look in-camera first. We will see where the technology goes!”
This feature was first published in the August 2024 issue of Definition.