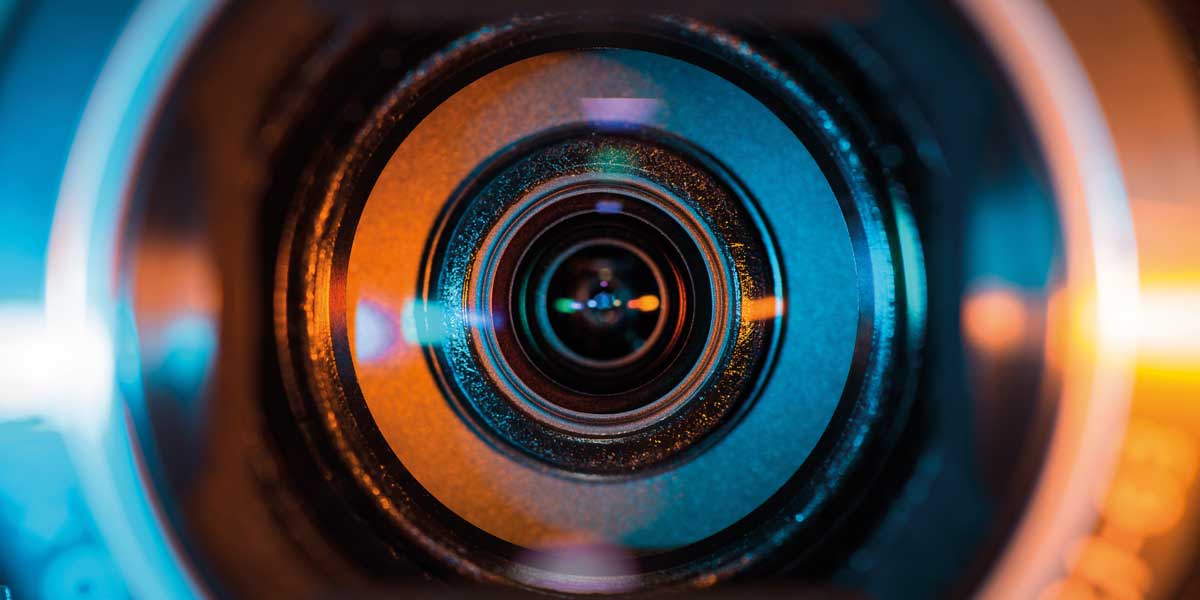
Round Table: Lenses
Posted on Sep 21, 2024 by Samara Husbands
What’s Next for Lenses?
Four experts zoom in on the future of optics, exploring recent key developments and predicting where lens technology might be headed
The Panel
- Dennis Meyer, Systems & development engineer – technology & innovation for
cine products, ZEISS - Sundeep Reddy, Product manager, digital cinema products, ZEISS
- Luke Cartwright,Product manager – optical devices, Fujifilm UK
- Seth Emmons, Director of communications, Ernst Leitz Wetzlar GmbH
Definition: What recent innovations in lens technology have had the biggest impact?
Dennis Meyer: The advancement in simulation tech has revolutionised the lens design process, enabling us to create and test designs in a virtual environment – a ‘virtual twin’ – before they are physically manufactured.
Another major innovation is the advancement in metrology, or measurement technology. This has allowed us to ‘close the loop’ with the virtual twin and simulation. By being able to measure and verify our designs with advanced accuracy, we can ensure that the physical product matches the virtual design as closely as possible.
These innovations have enabled us to deliver products faster and at a lower cost, without sacrificing high standards. For example, in the development of ZEISS Supreme Prime Radiance lenses, we were able to engineer the flare look using simulations. This allowed us to create a unique and high-quality lens family in a more efficient and cost-effective manner.
Luke Cartwright: Adaptable mounts within the mirrorless market, meaning endless possibility with your chosen camera brand. From the cinema and broadcast perspectives, though, the technology we’ve integrated into our premium broadcast and latest Duvo cinematic lenses have had a positive impact. We have Remote Back Focus technology, which means the back focus can be adjusted from the ERD-50 zoom demand or a robotic panel. But, from an optical perspective, we can use it to flatten out the optical performance where natural peaks and troughs form in a parfocal zoom lens, creating a sharp image anywhere in the range at all times.
Seth Emmons: The lens market seems to have pivoted away from innovations in technology, instead placing more importance on aesthetic character – particularly historical character. For decades, the job of lens designers was to make faster, smaller, more efficient lenses, but that’s not what DOPs are chasing these days. Uniqueness, style and creative options are often prioritised over technical performance.
Def: Are you seeing any notable trends with customers and in the broader market?
Sundeep Reddy: The creative process in the industry has seen huge changes over the last decade and a half, with filmmakers primarily shooting on digital cameras, larger formats, fast lenses, a variety of lens looks, lighter and smaller lenses for handheld work, VFX-filled productions and – more recently – the ever-growing need to shoot in virtual production environments which require metadata from the lenses. All of these requirements and more have pushed ZEISS to constantly innovate and keep abreast with trends. At ZEISS, we actively listen to market feedback, allowing us to plan well ahead. It’s fair to say we’ve been ticking most of the boxes well before they become trends.
LC: I’ve mostly noticed the move towards mirrorless in the professional cine market. The cameras and lenses are notably cheaper than your conventional cinema-style kit, but also have a much smaller footprint and weight. This means shooting possibilities can adapt and change without the need of large, heavy equipment to support the system.
We see many renowned companies introducing lightweight zooms and primes for the mirrorless cine market, and many smaller or up-and-coming companies coming in with amazing glass for a fraction of the cost. Another trend is the uptake in lightweight cinematic broadcast-style lenses, which we have answered with our Duvo range.
This workflow we see in live production and sports recently, where large-sensor cameras are used with broadcast-style lenses complete with typical OB trucks, is a positive change in shooting everyday sports and live events. We have seen a big uptake in the use of our Duvo range, which now has the 14-100 alongside the 24-300 and groundbreaking 25-1000.
SE: While there are still many DOPs who favour clean lenses and prefer building their looks more exclusively with lighting, set design and so on, the voices of those who want to start with a lens that has a strong look and then build on top of that are drawing more attention. This has created a trend which has trickled down to film students and aspiring cinematographers.
These ‘character’ lenses incorporate imperfections and optical flaws such as aberrations, distortion and flaring in ways that are visually appealing to the current artistic trends. Cinematographers seeking these lenses are no less skilled than those using cleaner glass; they’re simply asking the lens to do more of that work. The most successful production of these lenses is achieved in two ways: through rehousing older photo and cine lenses without optical modification for their client to preserve the original look; or through adjusting coatings, air gaps and/or swapping elements in old/new lenses, putting them in new housings, branding them and selling or renting them to clients.
While both processes involve significant skill and expertise in understanding how changes will impact the image, they don’t involve groundbreaking technology to create the specific visual performance. At the moment, both options are quite popular. Less impactful have been attempts to use advances in technology to create user-modifiable lenses that an end user or rental company can adjust themselves to change characteristics.
These work either through interchangeable parts in the lens itself, internal mechanical systems to adjust the image via air gaps, or adapters that modify the image between the lens and camera. Some companies are trying to incorporate even more technology into cinema production, but the response has been largely underwhelming.
Companies who are positioned in both the photo and video segments have started to push traditional photo system features like autofocus, face recognition and image stabilisation upstream, but they have yet to break through to higher market segments.
Def: How are lens companies adapting their product lines to meet the needs of virtual production environments, and do you have any advice for DOPs choosing lenses for VP?
SR: Lenses play one of the most vital roles in VP. They need to be calibrated or profiled accurately for a good, seamless VP experience. Quite a few companies have their own ways of calibrating or profiling lenses, but it is a time-consuming process. At ZEISS, thanks to our innovation, we have been able to eliminate calibration times when using ZEISS lenses, especially with our camera- tracking system CinCraft Scenario. A big enabler is having smart lenses on productions whereby metadata from the lenses can help feed rendering engines the data they need without having to reverse-engineer a lens.
LC: Lens-wise, my advice would be to go with a good-quality zoom lens, like the Fujinon Premista. With VP, there’s a lot of calibration time to take on board. Shooting with primes is very common in cinema, but when coupled with the time taken to calibrate lenses to virtual stages, we tend to lose time instead of gain it. Fujinon supported Mo-Sys on a project including green screen and LED screens, using two Premista 28-100mm lenses on identical camera set-ups side by side on each screen. Not only did this set-up show the pros and cons of two types of VP, it also highlighted the advantage of zoom lenses within these workflows. You can check out the full video on Mo-Sys’ YouTube in the future.
Def: Are emerging technologies like AI being integrated into lens design and performance optimisation? If so – how?
DM: We are using AI and machine learning for a lot of different tasks like data analysis, but not yet for actual lens design. Our lenses are designed by our talented and experienced engineers. Their expertise and hands-on experience is crucial in ensuring that the final output meets the highest standards of quality and performance – which no AI can do today. But it’s also clear that, in the future, AI tools will play a role in assisting our engineers with their daily work.
LC: They might be in other companies, but with Fujifilm/Fujinon we don’t use AI to design our optics, and don’t have any plans to do so. We have a computer – FUJIC – specifically designed and dedicated for optics design. We can input a number of data points, such as front lens diameter, focal length, weight, chosen T stop etc, to see what’s possible within our chosen size, weight, focal length and – most importantly – cost. It’s the first of its kind and was originally manufactured by Fujinon in 1956, since progressing into a much smaller, more manageable computer. The original is now in a museum in Japan!
Def: With the push towards sustainability, how are lens manufacturers innovating to create environmentally friendly products?
LC: Fujinon TV and cinema lenses are designed to last the test of time in all conditions, and we see it time and time again in the service department. Lenses in typically grubby conditions after a hard time on cinematic TV series in harsh environments; broadcast lenses back from big worldwide events, away for months at a time, only to find they need a dust down and the front and rear elements need cleaning. Having a reputable service centre that will keep you going long after a typical five-to-seven-year lifespan definitely helps old lenses in service and looking sharp.
In the early stages, we also have a very effective development process for new products, where we can really nail down the design without creating numerous pieces and keep material wastage at a minimum.
DM: For ZEISS, this is not a recent push, but a long-standing goal that’s deeply rooted in our company. ZEISS has been producing cine and photographic lenses for a long time – in fact, some of the lenses that we produced in the sixties are still being used now. Our lenses are known for their reliability and longevity, and we ensure service for used lenses long after we stop producing them, thereby allowing them to be viable in the long term.
Our internal requirements for materials and processes have always been ahead of their time, for example in not using glass containing lead. A more recent example is that ZEISS is proactively working to eliminate PFAS – known as forever chemicals – materials from all of our products, demonstrating our commitment to sustainability and product safety ahead of any enforced regulatory requirements.
Also, we have recently enhanced our cine lens packaging, transitioning to plain carton boxes and reducing plastic foam use, making our packaging fully recyclable and significantly lessening our environmental impact.
Def: What trends do you foresee in the future of lens technology?
SR: We’re working on a few great ideas we can’t talk about yet. But I would say that the focus should be looking at lighter, smaller smart lenses, but not compromising on principal features such as the look of the lens, a low T stop, build quality and mechanical performance – what creatives are looking for in a lens in the first place.
SE: How the industry and lens business will evolve from here is a big question mark. Manufacturers and rental companies are facing extreme pressure to provide products and services at lower costs with a preference for older aesthetics over new tech. The well-worn product management adage of ‘fast, cheap, good – pick two’ is still useful, but ‘good’ has become so relative that it’s almost an unusable metric, and ‘fast’ is only relevant to market demand.
Cost-efficiency has become the mantra of the industry and is disrupting the balance. If downward economic pressure continues to be the main driving force, we all face significant changes and challenges ahead – and technological innovation might not be the best way to weather the storm.
LC: Moving further towards smaller, lighter lenses, mirrorless mount options expanding and larger sensors in smaller bodies – something Fujifilm has been ahead of the curve on for a while now with the GFX medium format camera and recently announced upcoming GF cinema lens. It’s the same as cameras: UI systems becoming easier to navigate and better integration into third-party accessories creating workflows that quite literally are your mobile device. We’re at a pivotal point in TV and cinema where advancements in technology are coming thick and fast – Fujifilm is sticking alongside it with exciting new products and more in the pipeline!
This feature was first published in the October 2024 issue of Definition.