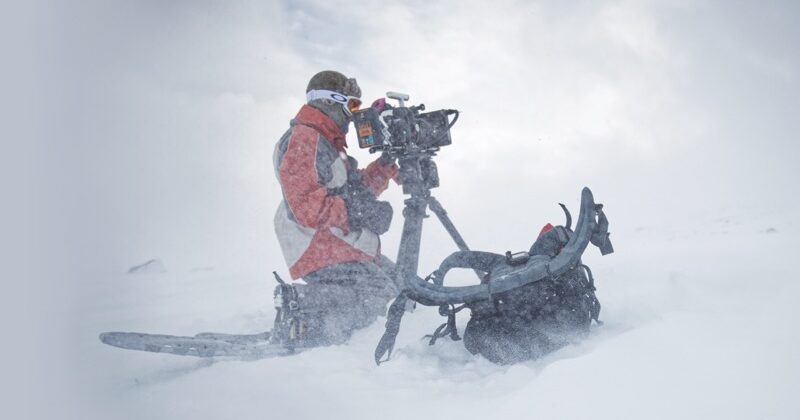
Round table: Batteries
Posted on May 10, 2025 by Admin
Experts from IDX, Hawk-Woods and NXTGENbps discuss industry trends and challenges, emerging technologies and the next big disrupter
The panel
- James Denyer, Key account manager, Hawk-Woods Ltd
- Lesley Marr, Director of sustainability & business development, NXTGENbps
- Koji Tsukada, Director, IDX Europe
DEF: What are the biggest challenges facing battery manufacturers right now when it comes to meeting the demands of film and television production?
Koji Tsukada: Compared to previous years, the cameras, monitors and lighting equipment used in film and TV production have become much more diverse, and product cycles have become much faster. We’re required to respond to the growing demand for high-capacity, highly durable batteries in line with the increase of high-power equipment that also demands support for long hours of shooting, as well as environmental impact, cost and safety aspects. IDX has a long track record in the global market, and is developing batteries that meet the needs of the field, comply with strict safety regulations from the industry and are manufactured under a rigorous quality control system.
James Denyer: As everything in our industry becomes more digitally advanced and intelligent, the battery market has seen significant changes in a short period of time. While the benefits of these innovations on-set are fantastic, they place a burden on battery manufacturers to cater to increasingly power-hungry equipment. This means all our designs must focus on the amperage demands and how we can provide that efficiently, within typical set constraints. It’s been a great challenge, which has pushed us to get more creative, not just within the batteries themselves but also with accessories like plates and cables.
Lesley Marr: The industry is now warming to the obvious benefits of more consistent, cheaper, cleaner, quieter power supplies – but location hire companies and studios face a major challenge. The initial investment, while existing fossil fuel stock is still functional, leads to a current lack of demand. This is despite battery generators being far cheaper to run and maintain than petrol or diesel ones. Manufacturers and distributors face a conservative attitude toward integrating new technology into familiar workflows – perhaps more so than in other industries.
Some operators are also reluctant to move to lower-power-consuming kit (lighting is a good example) instead of the higher-draw equipment they’re used to. Lower-power kit enables more efficient battery use and reduces the production’s carbon output. Safety concerns, often due to uncertified batteries – like e-bike cells – have given batteries bad press. Li-ion types can pose risks if damaged or mishandled. At NXTGENbps, our use of LiFePO4 and solid-state chemistries helps reduce this risk.
All our batteries carry CE certification and markings – it’s a costly process for manufacturers but essential to reassure users. There’s also the logistics challenge as, instead of one large diesel generator, crews might need to move multiple batteries. Balancing portability, power and weight is crucial – but using the right batteries can reduce cabling and carbon output and improve crew wellbeing.
DEF: How are evolving camera and lighting technologies influencing the design and performance requirements of batteries?
JD: The rapid evolution of camera and lighting technologies is significantly affecting battery design. As new kinds of equipment demand more power, we’re constantly exploring how to meet that need within the environmental and spatial constraints of a set. Batteries now have to deliver more efficient power at higher capacities, and we’re also working closely with accessory manufacturers to support these technologies.
KT: The latest cinema cameras and LED light sources are becoming more powerful and more efficient. As a result, batteries need to supply higher currents and operate for longer periods.
In particular, the spread of 48v LED lighting and 28v cameras means that a more diverse product range is required. IDX recognises that higher-voltage and higher-capacity solutions are essential for improving convenience in film and TV production, so it has introduced 28v solutions as well as taking steps to develop products that can keep up with the ever-changing technical landscape.
LM: The use of high-kilowatt-output tungsten lighting draws more power than similar LED lights, and a common DOP creative debate is whether the look of tungsten can be matched with LEDs. But trends are changing, and DOPs with sustainability ethics are moving towards LEDs, which have reduced power draws and therefore enable smaller batteries to be deployed – reducing the use of large diesel or HVO generators.
Battery manufacturers have listened to the production community, bringing out mobile units with power levels in the sweet spots of 3, 5, 10 and 15kWh. These are more desirable and affordable for rental companies than larger, non-mobile options, and can be daisy-chained to create bigger power banks. It just requires more planning and monitoring, which is a shift from the one-size-fits-all generator typically used.
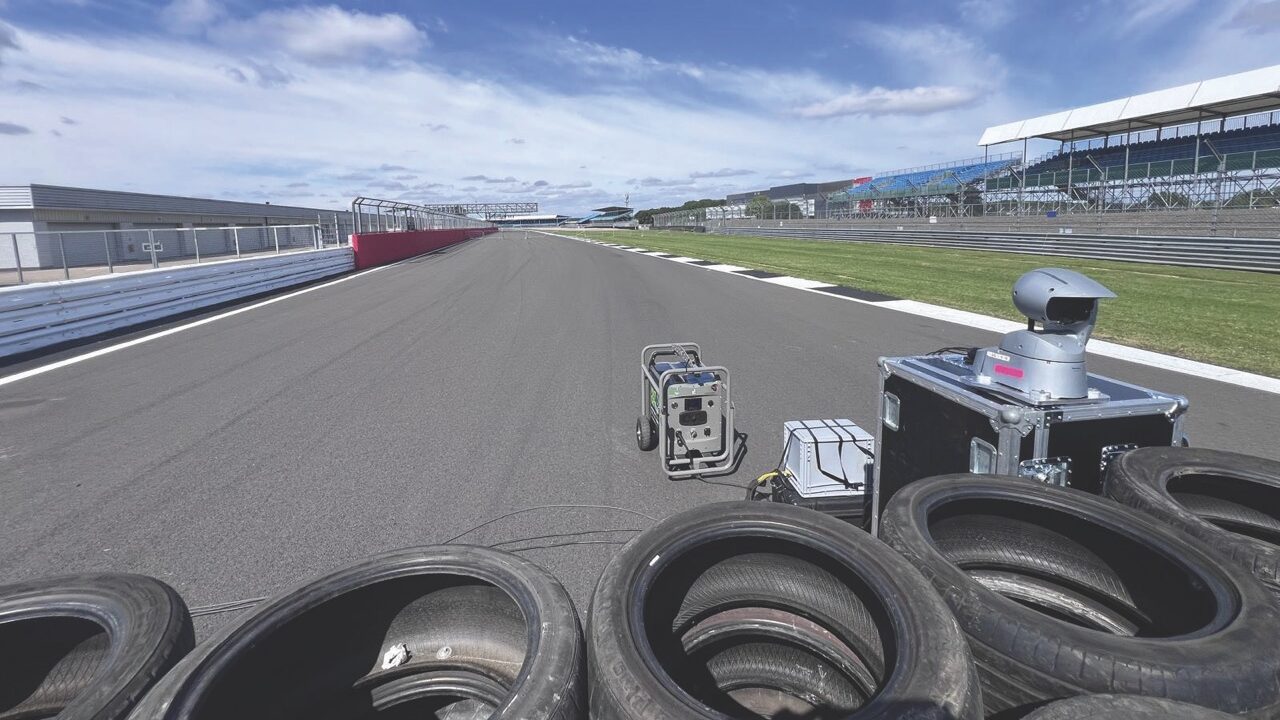
DEF: What strides are being made in battery tech and manufacturing to reduce environmental impact?
KT: Reducing environmental impact is a crucial issue for the industry as a whole, and IDX is actively promoting the refurbishment and recycling of disused Li-ion batteries in the Japanese market. As further battery regulations are also due to come into force in Europe, we intend to actively promote and implement it within this region as well.
In terms of our products, some models include a function that monitors battery degradation in real time, notifying the user of the degree of degradation and thereby preventing premature disposal. The manufacturing process is also becoming more efficient to reduce the environmental impact. Specifically, we’re working to reduce the use of rare metals and – in future – we plan to use next-gen technology to produce batteries with a lower environmental impact.
JD: The global demand for lithium is rising, largely driven by the EV industry. As it’s a limited resource, we’re committed to ensuring that lithium doesn’t end up in landfill. There have been great strides in lithium recycling, and Hawk-Woods, in partnership with our group UPERGY, has collaborated with global specialists to reclaim and reintroduce lithium into the market, reducing the need for new mining. To encourage the return of old batteries, Hawk-Woods has also introduced a trade-in scheme, offering discounts on replacement batteries. Our goal is to remove excess old Li-ion batteries from the industry and ensure they’re properly recycled.
LM: Working with truly recyclable cell types, such as lithium iron phosphate, is a huge step forward. Ensuring the battery generator can accept solar charging and has a long working lifetime also genuinely makes the product better for the environment. Unfortunately, many cheaper consumer batteries still use non-recyclable lithium, have short lifespans and require non-renewable charging – these often end up in landfill far sooner than expected.
Sodium-ion is gaining attention as an alternative, since sodium is more plentiful and less toxic. However, Na-ion batteries have lower energy density and shorter life cycles – and are generally better suited to stationary applications. Solid-state batteries are more promising; they use solid electrolytes instead of liquid, reducing the use of harmful solvents. Our new Swift battery, which will become available this summer, is flight-safe – one of the first of its kind.
Battery recycling – reclaiming nickel, lithium, cobalt and graphite from old batteries – also continues to improve. Some EV batteries are now being reused in stationary energy systems, giving them a second life before disposal to reduce their environmental impact. Our NXTGENbps batteries are upwards of 95% recyclable – a key factor we look at when deciding which products to stock.
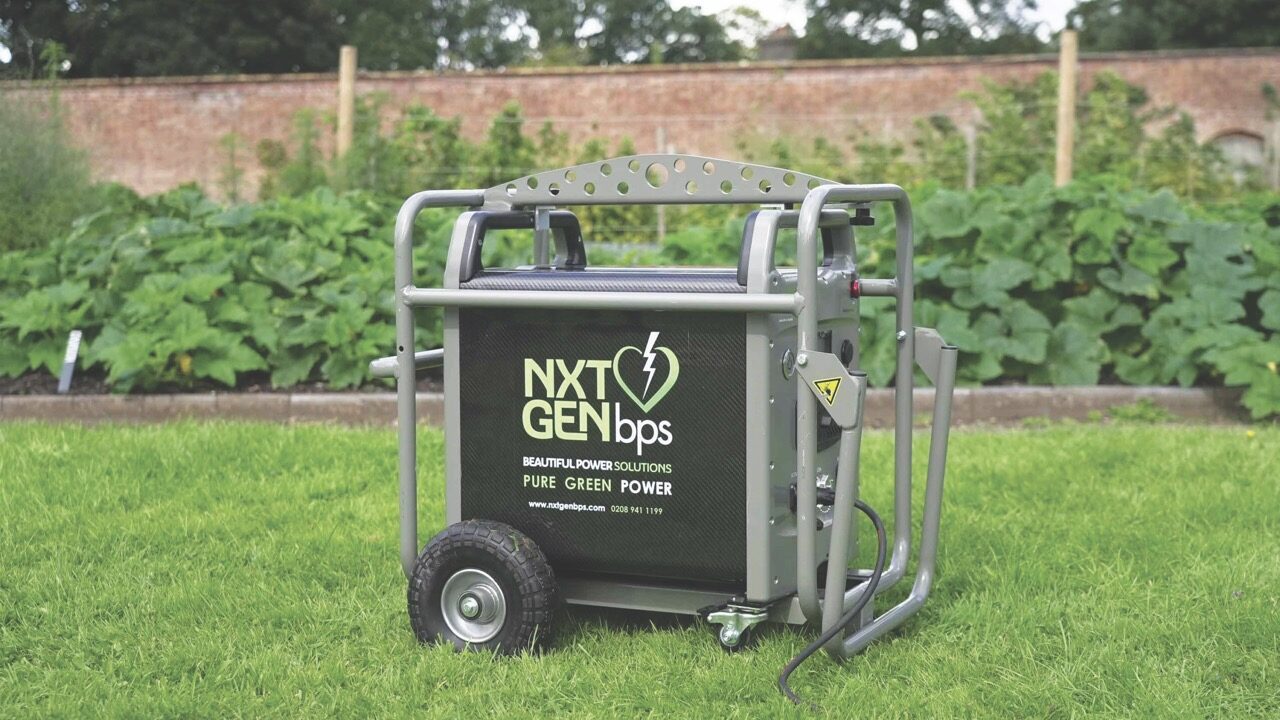
DEF: What emerging battery technologies do you think will have the most practical impact on film production in the next few years? Are there specific breakthroughs on the horizon that filmmakers should be excited about?
JD: Much of the development in this area is currently being driven by the EV industry, rather than directly by film production. Currently, lithium-ion remains the best option in terms of its power output and capacity, with newer cells still not able to match its performance. However, we’re seeing improvements in Li-ion technology, with smaller and more powerful cells being developed. As the EV industry continues to innovate, we can expect these advancements to eventually be adopted by the film industry too.
LM: At NXTGENbps, we’ve just launched the world’s first nickel manganese cobalt (NMC) solid-state battery – the Swift. This type is both extremely lightweight and extremely stable, which allows it to be flight-safe. It will have a big impact on productions that travel to remote and harsh locations to film. Our batteries are IP67-rated and fully weatherproof, so can be transported to and used even in the harshest environments.
From years of working with film and TV crews, we know only the most robust kit survives, as equipment is constantly moving. That’s why casing and material choices are so important. I don’t believe sodium or hydrogen are currently suitable enough for TV and film use. Small and mid-sized mobile batteries with solar compatibility are much more cost-effective and flexible. Since more equipment now includes wireless control, smart battery tech is also becoming relevant. Our Swift battery, for example, has built-in communication capabilities and connects to an app that allows users to monitor charge status, battery health and power levels remotely. This supports power planning and on-set logistics. Using more solar will also have an ongoing impact in terms of reducing carbon emissions. Flexibility, portability and smart functionality are the directions that battery tech needs to keep moving in to support film production.
KT: Regarding the battery itself, we believe new cell technologies with high energy density will have a significant impact on future film production. For example, improved cell tech has the potential for better safety and energy density, and could then lead to more compact, higher-performance batteries with dramatically improved discharge and charge performance. IDX was the first in the industry to commercialise the battery pack using Li-ion cells in 1996, and through the decades this has evolved. Our batteries now feature USB PD connectors to be in line with consumer electronics, allowing users to charge via general-purpose devices. Of course, IDX will continue to innovate and actively adopt new technologies in the future, so we can continue meeting customer needs and requirements.
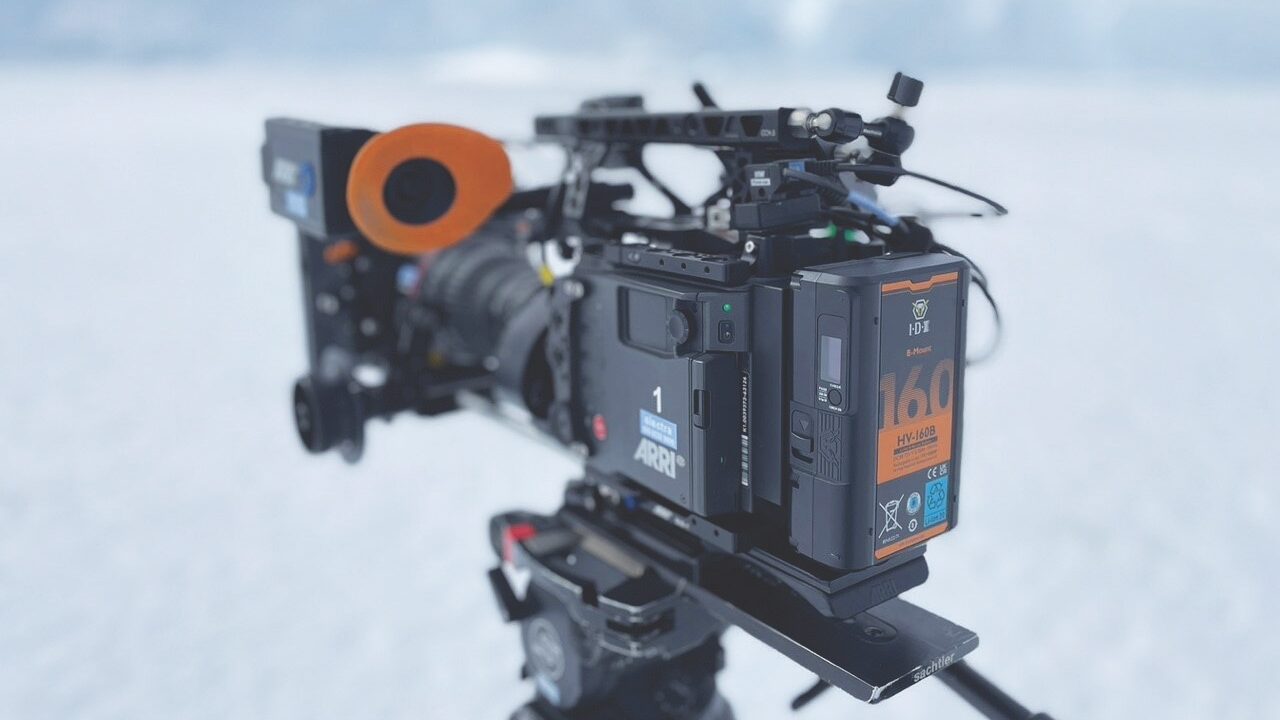
DEF: When it comes to battery safety and reliability, what common mistakes do you see crews making, and how can they avoid them?
JD: Charging is the most-common issue I see. The analogy I use is to think of a battery like a balloon and the charge as air being blown into it. It’s easy to add air at the start, but as the balloon fills it becomes harder to add more, creating strain. The same happens with a battery. The biggest mistake is leaving a unit at full charge during prolonged storage. This can degrade the cell’s health. If storing a battery for a longer period, we recommend maintaining a charge between 40% and 60% to reduce strain and prolong the battery’s life.
LM: It’s mostly about storage, handling and choosing the right battery in the first place. While good-quality batteries have wide operating temperature ranges, getting the most out of them requires proper care. They should generally be stored in a cool, dry place – not left in direct sunlight or extreme heat. It’s also important to invest in certified batteries with a good IP rating from a reputable, professional-use manufacturer.
We’ve seen several customers who had bought consumer-grade batteries for DIT or location work, only to find they had poor life cycles, weren’t robust and couldn’t support renewable charging. Crews also need to think more about power planning. Understanding equipment power spikes – especially during start-up – helps ensure the right batteries are used to avoid frequent swaps. This wasn’t always necessary with a large diesel generator covering everything, but batteries require a more tailored approach.
Most good batteries now offer backup or daisy-chain options. For example, our SHAPE Basecamp Emperor battery has a 15kW output and can be paired with a 15kWh backup unit – up to 20 can be daisy-chained. Our 5kW Goat battery can be used with a 9.6kWh Billy Goat backup too. Matching the battery capacity to the kit and allowing some headroom makes all the difference.
KT: Ultimately, IDX batteries are designed, built and tested to the highest standards possible, and all our batteries feature several safety protection circuits to reduce any potential concerns that customers might have. This allows us to ensure that all of our products are safe for professional use in a variety of environments, as well as in complicated or demanding work situations.
However, the common mistake that should be avoided is leaving batteries on equipment when they aren’t in use. Leaving batteries on equipment, even when it’s switched off, can increase the natural discharge rate of the battery. Additionally, if a fully discharged battery is left on the equipment, this could potentially discharge below the minimum voltage and therefore might not be recoverable!
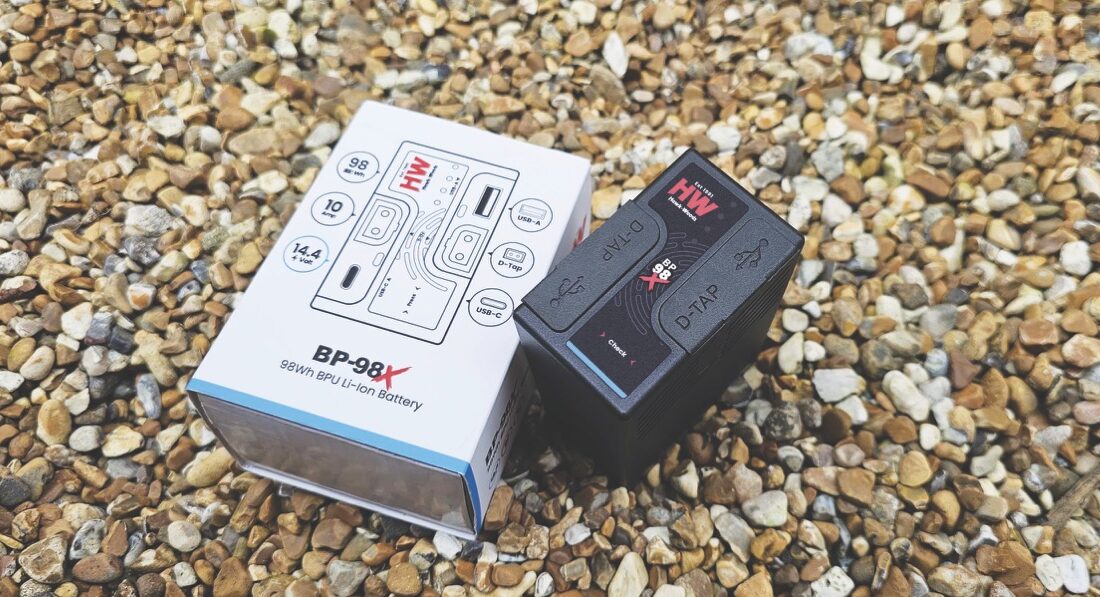
DEF: What advice would you give to filmmakers who are looking to optimise their battery investments over the long term?
JD: Battery storage is essential for extending the life of your equipment, but another great method is hot-swapping. By swapping over batteries while in use, you can maintain their performance and avoid placing unnecessary strain on individual cells.
LM: Look for battery generators with a long working lifetime to ensure return on investment. Are the cells stable – like lithium iron phosphate or NMC? These chemistries offer upwards of 4000 cycles, which can provide ten to 15 years of use.
Also, be sure to check whether the battery includes an inverter. Inverters allow for different charging methods to be employed, like solar or EV, which reduces the running costs and speeds up charging. They also help manage input and output power to prevent overheating and extend battery life.
Always invest in certified batteries with a good IP rating from a reputable manufacturer. Cheaper products aimed at the leisure market typically don’t stand up to the demands of production.
Finally, test and understand the power output of your equipment. That way you can be confident in what your battery system can support on-set – and avoid any range anxiety.
KT: Using safe, secure, proven and reliable batteries will optimise your investment in the long term. With such a wide variety of batteries on the market these days, it’s important to research the one you’re purchasing. Has it been manufactured ethically, has it passed the required safety certifications and are the power requirements suitable for your chosen equipment?
Once you’ve invested in your battery kit, the important thing is to know how to properly store them. Batteries shouldn’t be left on equipment for extended periods of time if not in use (whether you’re charging or discharging). If being stored for a longer period of time without use, they should be left at approximately 50% charge, to slow the discharge rate. IDX batteries have technology installed to slow the natural discharge rate down, however this can never be stopped entirely with Li-ion batteries. We include storage guidance on our website – as well as in the manuals – for every battery we produce, to make sure customers are getting the most out of their investment.
DEF: Looking ahead, do you see any major disruptors – whether regulatory, technological, market-driven or anything else – that might significantly alter the battery landscape for filmmakers?
JD: Lithium-ion batteries are increasingly under scrutiny, with real concerns about environmental impact, insurance and shipping regulations. These factors could have a significant influence on the battery landscape in the near future.
KT: This is not limited to our industry, but the impact of stricter regulations is inevitable. At IDX, we comply with different regulations in each region, and battery regulations in Europe are moving in the direction of becoming ever stricter.
With increases in battery size and capacity, the biggest challenge will be navigating the current shipping restrictions and ensuring we can find a practical, dependable method to ship these goods. Whatever the future holds, we’ll continue to work hard to comply with regulations in each region and deliver the same level of safety and security to our customers as we have done in the past.
LM: Hopefully, government assistance with the transition from fossil fuel to battery generators. The switch would be smoother and quicker if companies could be supported – potentially through tax incentives or grants. It would benefit everyone, including the government, to reduce reliance on fossil fuels and move towards clean battery power.
Battery technology is already there – we have secure, powerful, flight-safe, weatherproof batteries ready to deploy. But support from policy and regulation would accelerate their adoption by those rental houses and location providers still working with diesel fleets.
For more insights into the industry, read Round Table: Virtual production.
This story appears in the April 2025 issue of Definition